Monday, February 28, 2022
& How to Fix Them
Every rotary instrument at some point in its life will become noisy and clanky. It is a simple fact of life - as metal wears and tolerances open up, valves have more room to wiggle around and make noises. Just like a small hit from a hammer at low height produces very little noise, a hard hit from a bigger height produces a much bigger noise. This is the same principle happening in a rotary valve. Sometimes, the problem is so exaggerated that you can literally shake the horn and hear the valves beating around inside the instrument!
So, what causes a valve to go out of tolerance? Quite simply, it is a by-product of the aging process. Like an old worn-out engine, the bearing surfaces in a rotary valve wear over time causing wider and wider tolerances between the casing and the rotor itself. One thing you may have heard to do is use heavier oil - although this works it is only a short-term solution. But what if I were to tell you there was a better, more permanent solution?
There certainly is! Rotary valves have bearing surfaces that can be tightened through a process called "swedging" and through removing material in the bearing plate. Sound counter-intuitive? I will explain.
There are two types of play that we remove in a bearing refit:
- Side Play, or the amount of side-to-side play a rotary valve has in the tapered bearings.
- End Play, or the amount of up-and-down movement a rotary valve has in the casing.
Want to know more about the process? Click below for a YouTube video I made detailing the process.
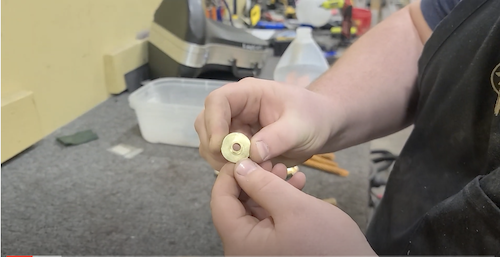
If a rotary valve is in good shape to begin with, having no damage to the bearing plate or chimneys then this process is a relatively simple one and not terribly expensive. I charge $30.00 per valve on French Horn and Trombone, and $50.00 per valve on Tubas. This process can add years of life to a rotary valve before the decision must be made to plate the valves or replace the instrument and is a service that every school with an aging fleet should consider looking into having done.
![]() |
Corey Divine graduated from the University of Arkansas in 2015 with a double major in trumpet performance and music education. During his time at the University of Arkansas, Corey performed with numerous top University Ensembles, the Symphony of Northwest Arkansas, the Arkansas Philharmonic Orchestra, and the Fayetteville Jazz Collective. In addition to his studies at the University of Arkansas, Corey began repairing musical instruments in 2012 under the tutelage of Chase Cavalier. He specializes in brass instrument repair and restoration. Corey began fixing things around the house at a very young age and has always been a tinkerer with a curious mind. Most people have hobbies, but Corey enjoys instrument repair so thoroughly that he hasn't worked a day since beginning his career. Corey's interests include collecting Conn instruments, building Frankentubas, and spending time with his dear wife, two sons, and three dogs. |
Click below for a video review of the Keilwerth SX90R Professional Alto Sax
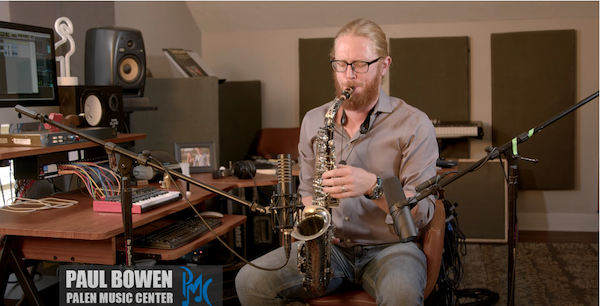
(417) 882-7000 | (573) 256-5555 | (816) 792-8301 |
(417) 781-3100 | (405) 896-8111 | (479) 464-8877 |
(918) 286-1555 | (636) 229-1904 | (417) 882-7000 |